Yards
Icon of the Seas
The largest cruise ship so far
photos: ROYAL CARIBBEAN INTERNATIONAL
The first in the series of Royal Caribbean Internationals new cruise ships – Icon of the Seas – is under final stages of construction at Meyer Turku shipyard in southeastern Finland. Delivery is scheduled for October 26, 2023. When ready, the new ship will be the largest cruise ship in the world by gross tonnage.
In the city of Turku, Meyers shipyard
has lots of experience for building ultra
large luxury cruise ships. Many of them
rank among the largest ones ever built
anywhere.
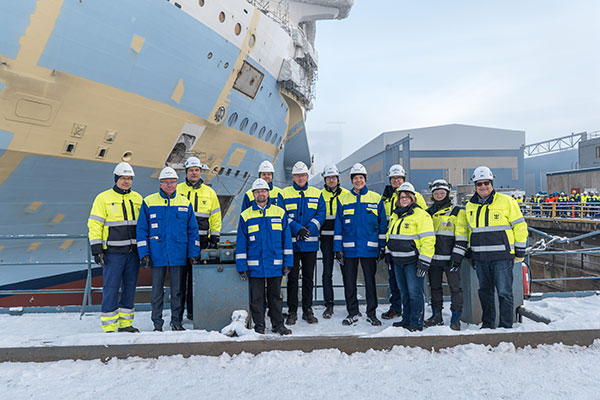
Royal Caribbean Internationals Icon of the Seas reached its next major construction milestone
at the Meyer Turku shipyard, when it was floated out of the dry dock and into its outfitting
dock in December 2022. Tim Meyer, CEO, Meyer Turku and Harri Kulovaara, executive vice
president, Newbuilding, Royal Caribbean Group, marked the occasion in Turku with the team
of innovators working on the revolutionary, new ship.
photo: MEYER TURKU OY
In the case of Icon of the Seas currently
undergoing the last bouts of installation
work, Meyer Turku shipyards Project
Manager Olli Jantunen notes that
the ships interior assemblies, as well as
the installations of electrical and automation
systems, are now proceeding rapidly.
Finishing touches will be underway
presently. In recent times, we have been
preparing the ship for the first open-sea
tests that have been scheduled for mid-
June.
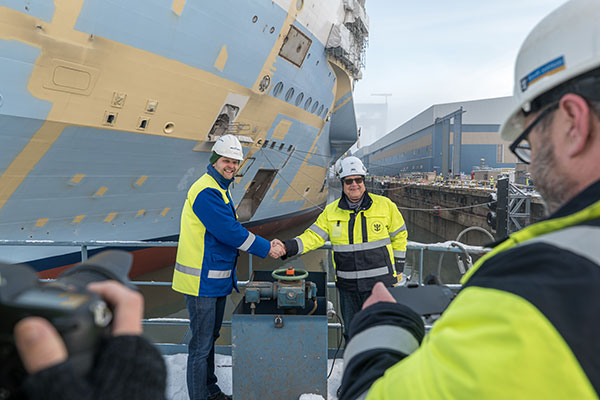
photo: MEYER TURKU OY
The ship will be powered by liquefied
natural gas (LNG) or alternatively diesel
oil, having six Wärtsiläs Dual Fuel engines
installed. Additionally, fuel cell technology
will be utilised to produce electricity and
fresh water.
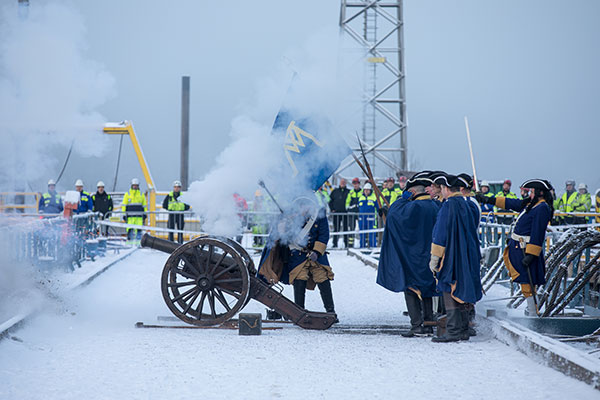
photo: MEYER TURKU OY
INTRODUCING THE AQUADOME
The prominent Aquadome structure on top
of the ships top deck has been designed
for arranging water acrobatics shows while
the area also includes a bar with a 220
degree ocean view, shops and dining venues.
The dome was manufactured as a prefabricated
modules at Meyer Turku shipyard
and lifted in one piece onboard the
vessel where it landed on 4th November
2022.
Installation work of the Aquadome
interior and systems is progressing on
schedule. The Aquadome is the most
demanding area of the vessel from a shipbuilders
point of view. It is a very technical
space with lots of moving parts, incorporating
44 different systems to be commissioned
– sort of a project within the project,
Mr. Jantunen points out.
The Aquadomes glass sphere is 55
metres in diameter, but it has no intermediate
support pillars. The base of the dome is welded onto the ship, but the upper
levels are connected with flexible joints.
The world class steel-designing team of
our shipyard has strongly contributed to
the finalisation of the domes structures.
MODULAR EFFICIENCY
In addition to the Aquadome sphere, the
ships hull in way of the LNG fuel tanks
– including the LNG tanks themselves –
was prefabricated in Germany as a floating
ship piece.
Furthermore, the engine casings
including all equipment ventilation and
sprinkler tubes, catalyzers, noise mufflers
etc., are also prefabricated modular structures.
The ship has an exceptional number
of prefabricated technical modules: 1 710 in total, of which 1 650 have already been
installed. Ready-made units help to make
the shipbuilding work more efficient, Jantunen
explains.
Even the 15 of the 19 on-board service
elevators are of plug-in type. The first
three of them were ready for production
use onboard in April 2023. In May, a total
of ten service elevators are already operational,
helping out in the transport logistics
of construction work.
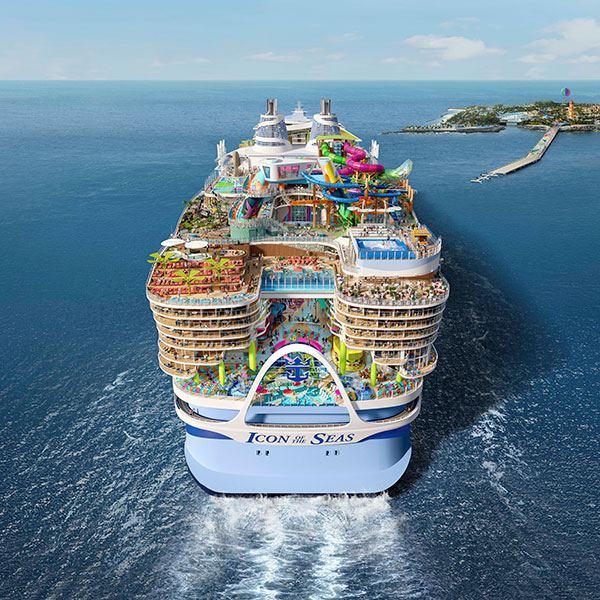
HUGE DIMENSIONS
The main dimensions of the ship had
already been determined when the ship
was ordered, i.e. before the shipbuilding
commenced. However, the Covid-19 pandemic
brought about a delay of 18 months for the project. This gave the ship designers
an opportunity to fine-tune certain
design features and architectural concepts.
Also, the ship became somewhat
larger than originally planned. Now she
will have a gross tonnage of 250 000,
which makes the Icon of the Seas the largest
cruise ship in the world.
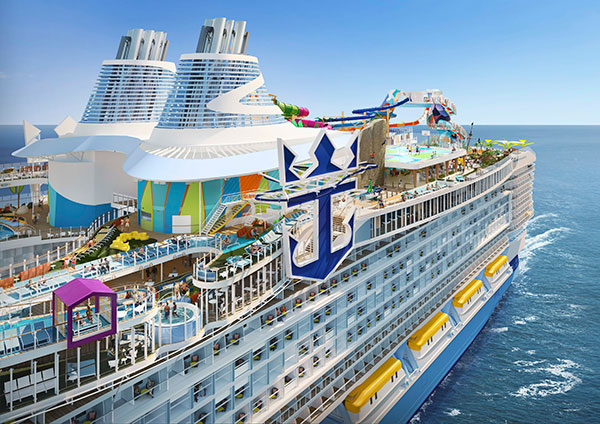
The ship will have more than 20
decks, a length of 365 metres and a
speed of over 22 knots. The 2 813 cabins
on board will have the capacity to house
a maximum of 7 600 passengers.
Once completed and delivered from
the shipyard in the later part of October,
the ship will be offering cruises in the Caribbean
Sea from Miami, Florida, from early
2024 onwards.
OPTIMAL PERFORMANCE
According to Mr. Jantunen, shipbuilding
work for the largest cruise ship in the
world has been a technically demanding
project.
The ship will incorporate huge
amounts of state-of-the-art technology. Furthermore, what we have here is also
the worlds most energy-efficient cruise
ship, he recounts.
Environmental emissions of the ship
have been minimised. A lot of work has
been done to optimise the hull shape of
the vessel, in order to make the sailingresistance
factors as minuscule as possible.
Additionally, the ship has an air lubrication
system to lower friction as the ship sails.
The energy consumption of the vessels
systems is dynamically optimised. For
this purpose, Meyer Turkus own dynamic
simulation model was used.
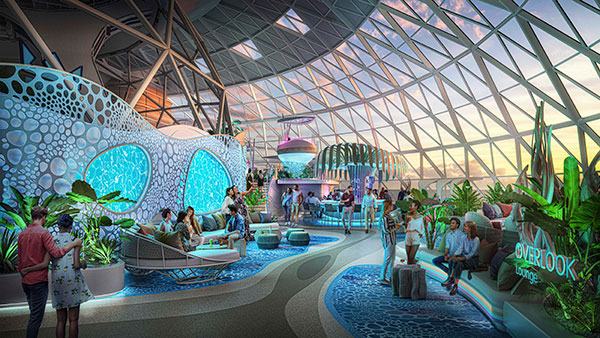
The dynamic simulation model contains
all the ships equipment and consumers,
and it enables us to phase-optimize,
already in the design, the energy-efficiency performance on the actual routes where
the ship will be operating – in this case,
particularly in Caribbean conditions.
To further improve the energy-efficiency
of the ship, the surplus energy of
the LNG-fuelled engines will be utilised to
produce steam for use in the steam turbine
that produces six percent of the electrical
power needed aboard the ship.
Also, the ship is equipped with
absorption coolers, to produce air-conditioning
systems with cooling energy, Jantunen
mentions.
Efficiency and automation of the airconditioning
has also been improved to
save energy.
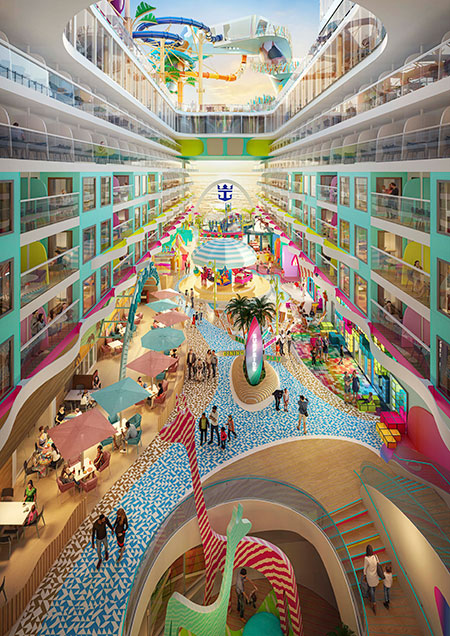
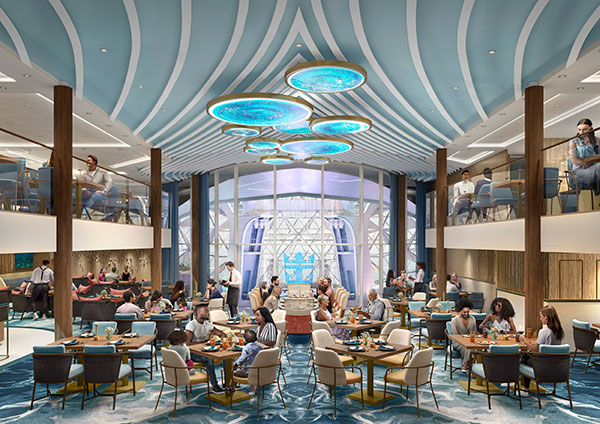
MORE SHIPS TO FOLLOW
Royal Caribbean Internationals series of
Icon-class cruise ships will be completed
by two further vessels to be built by Meyer
Turku shipyard and to be ready for use in
2025 and 2026, respectively. Shipbuilding
work for the second ship was already
started a few months ago, both at Turku
shipyard and – to produce the floating LNG
fuel tank part for the ship – at the Neptune
shipyard in Germany.
The following two ships in the series
will be built largely in the same way as the
first platform, but some new developmental
features may be added along the way,
Jantunen expects.
For Icon of the Seas, a workforce of
several thousand people took part in the
shipbuilding project, some of them representing
any of the almost 1 000 subcontractor
companies involved.
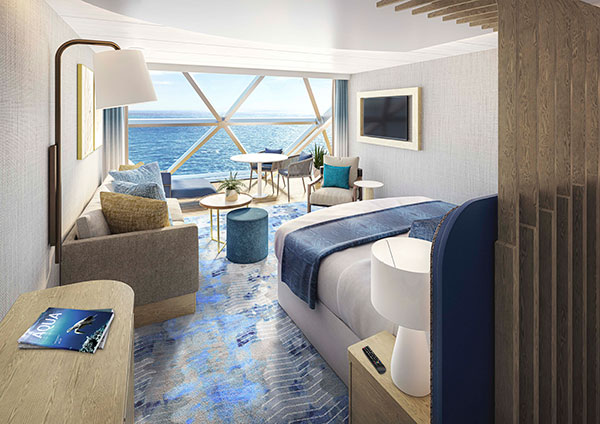

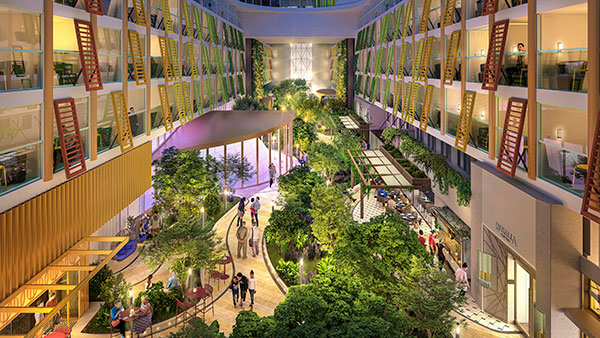
The next step for finalising the Icon
of the Seas will be to prepare for the imminent
open-sea tests to be carried out in
early summer of 2023. Commissioning
tests are already being conducted upon
various technical equipment and devices.
As an example, the propulsion systems have already gone through a preliminary
start.
The main engines will undergo
loading tests. Further tests will focus on
automation systems, safety systems, and
propeller functionality, says Jantunen.
The first open-sea tests will be relatively
short in duration, lasting perhaps
a few days.
It is always challenging and exciting
to run open-sea tests on a vessel that is
the first one in a new series. In a way, she
is still kind of a prototype. Things appear
to be going smoothly, but it is always prudent
to prepare for unexpected events, just
in case.
by: Ari Mononen